DESCRIPTION
Rubber removal is a process, involving high pressure water, to remove the rubber from tires that builds up on airport runways.
The global process made by our technicians includes the following steps:
Rigorous preparation before starting
an on-site visit from our airport services manager;
assess starting friction coefficient values;
transport the equipment to the site;
Professional rubber removal operations and quality monitoring
Taking a full array of measurements and analyzing the results;
Create a grid to cover the areas to be treated;
Pressure cleaning and feed-back on a test zone;
Complete runway rubber removal process, followed by an expert technician;
Grip evaluation, if possible;
Remove and processes the waste water and rubber;
Certification of the works
Delivery of an operation report and a certificate of compliance for the runway.
The RODECO-SUEZ Technology operates with different specified trucks, having the following features:
Length: from 12 m to 16.50 m;
Rubber removal width: from 1.4 m to 2.45 m;
Fresh water tank dimension: 8-9 m3;
Waste water tank dimension: 10 m3;
Working hours for each fresh water content: 3 hours;
Maximum removal speed: to 75 m/min;
Performance per hour: 2500-3500 m² (depending to the rubber thickness);
Water flow: from 20 to 90 l/min;
Water pressure: da 1000 a 2500 atmosphere.
Some trucks are equipped with an integrated water recycling system to increase work autonomy and minimize water consumption.
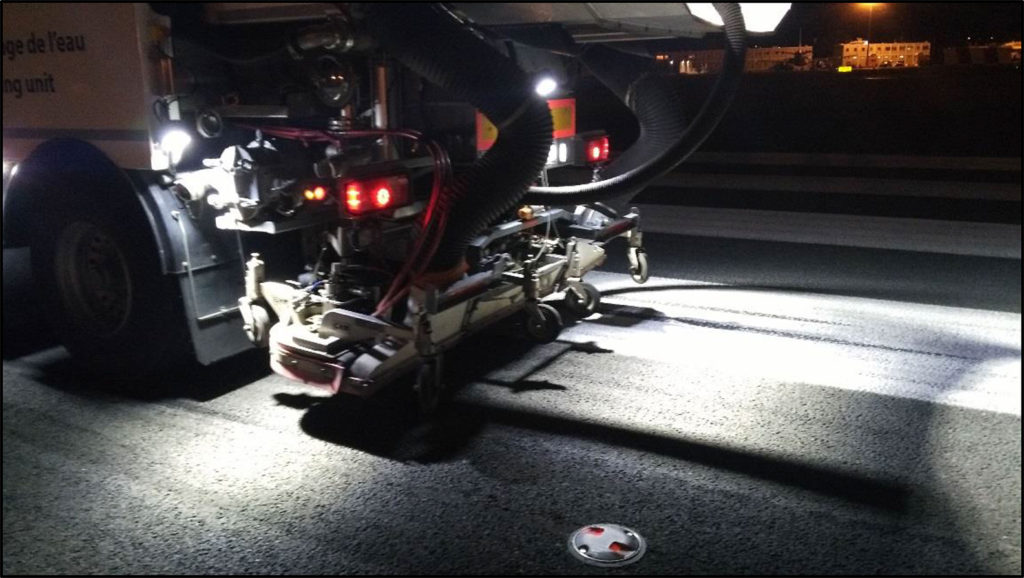
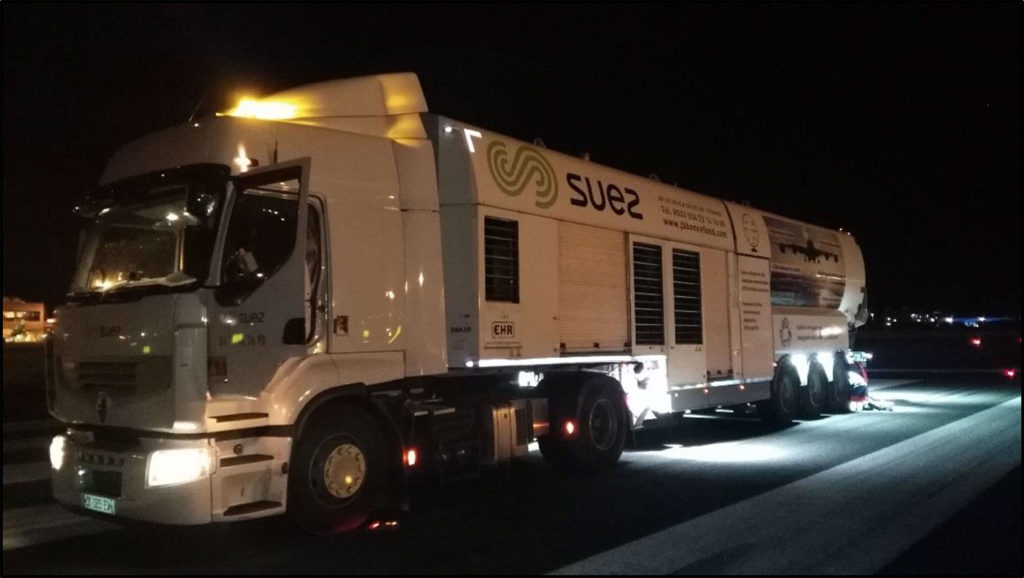
MICRO & MACROTEXTURE INCREASING
This process involves blasting pure water under high or ultra-high pressure (1,000 to 2,500 bars) on the runway pavement with the use of rotating booms equipped with specific jets.
The technique used alters and improve the micro and macro-texture of surface courses, with the following adding benefit:
Increase the skid resistance;
Extend the life of the surface course;
Restore the pavement safety.
This eco-friendly work method is the only one with no added material. This technique only uses water projected at very high speed in order to remove bitumen bleeding.
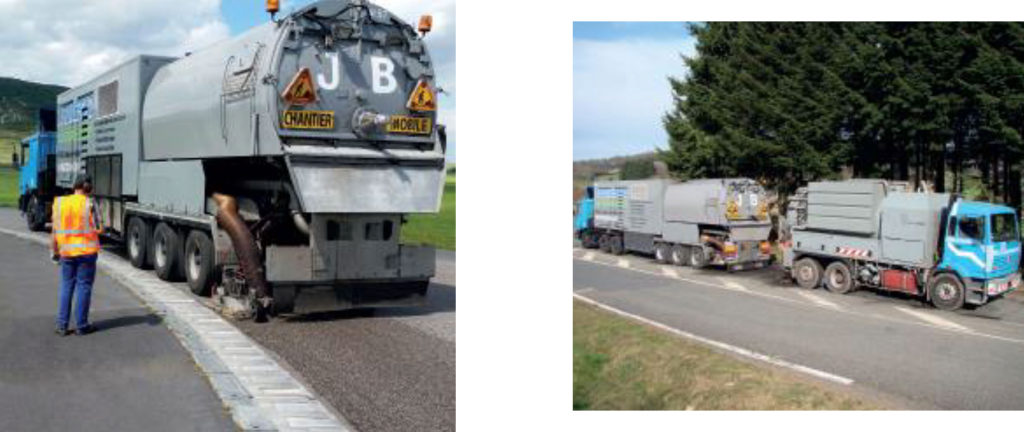
The technology proposed is the Rugor trucks, that has the following features:
6-axle semitrailer, including 3 directional axles at the rear;
WOMA 600 hp UHP pump – 1,000 to 2,500 bars, 40 to 108 L/min;
Stripping carriage fitted with 4 rotary heads, Ø 50 cm;
Mechanism to adjust carriage movement outside of the vehicle’s clearance dimensions – approx. 50 cm (20”);
Suction turbine, 20,000 to 30,000 m3/h;
Water filtration/recycling device for rubber residue removal work.
Advantages:
Powerful UHP pump highly suitable for elastomer-modified surface dressings;
High rates achieved on bituminous mixes or runways with the use of the water filtration/recycling system;
All-in-one equipment ensures stripping, suction and recycling.
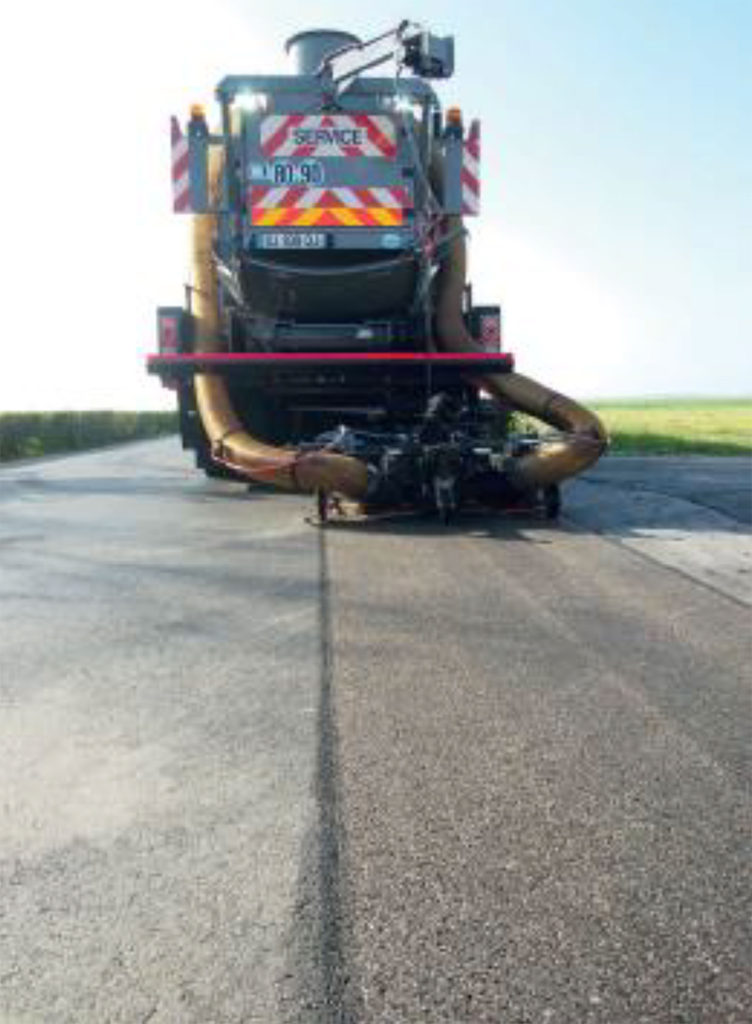
PAINT REMOVAL
The machine is the same used for the rubber removal, adding a special mechanical extension in front of the truck, for the removal of the linear markings.
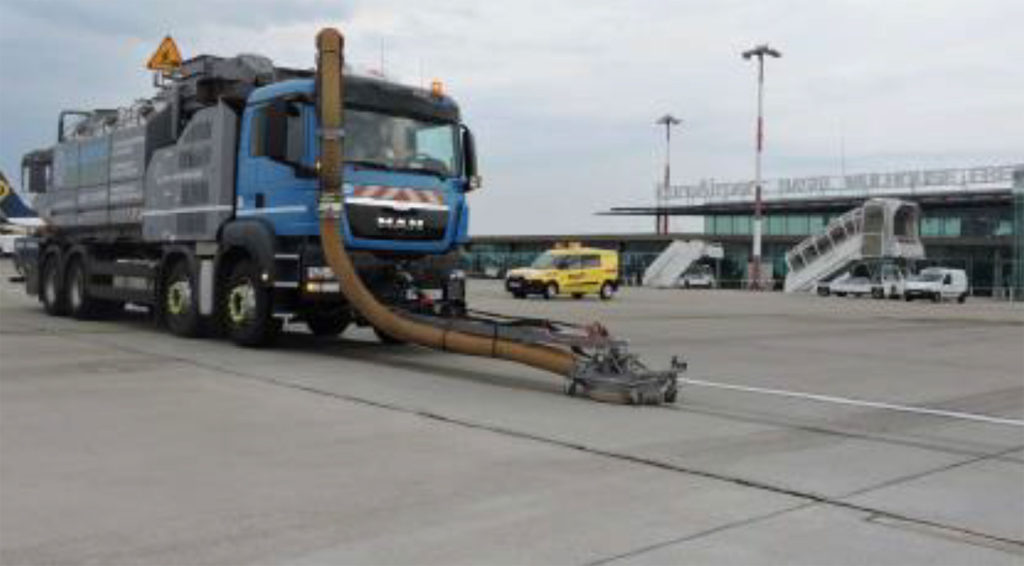
The feature of the painting removal system are the following:
Painting removal width: 0.35 m;
Working hours for each fresh water content: 4.5 hours;
Performance per hour: 100 m² (depending to the marking thickness);
Water flow: 40 l/min;
Water pressure: 2500 atmosphere.